Parametric Study of Flexibility Factor for Curved Pipe and Welding Elbows
SMiRT-22, San-Francisco California USA, August 18-23 2013, FLEXIBILITY_PAPER
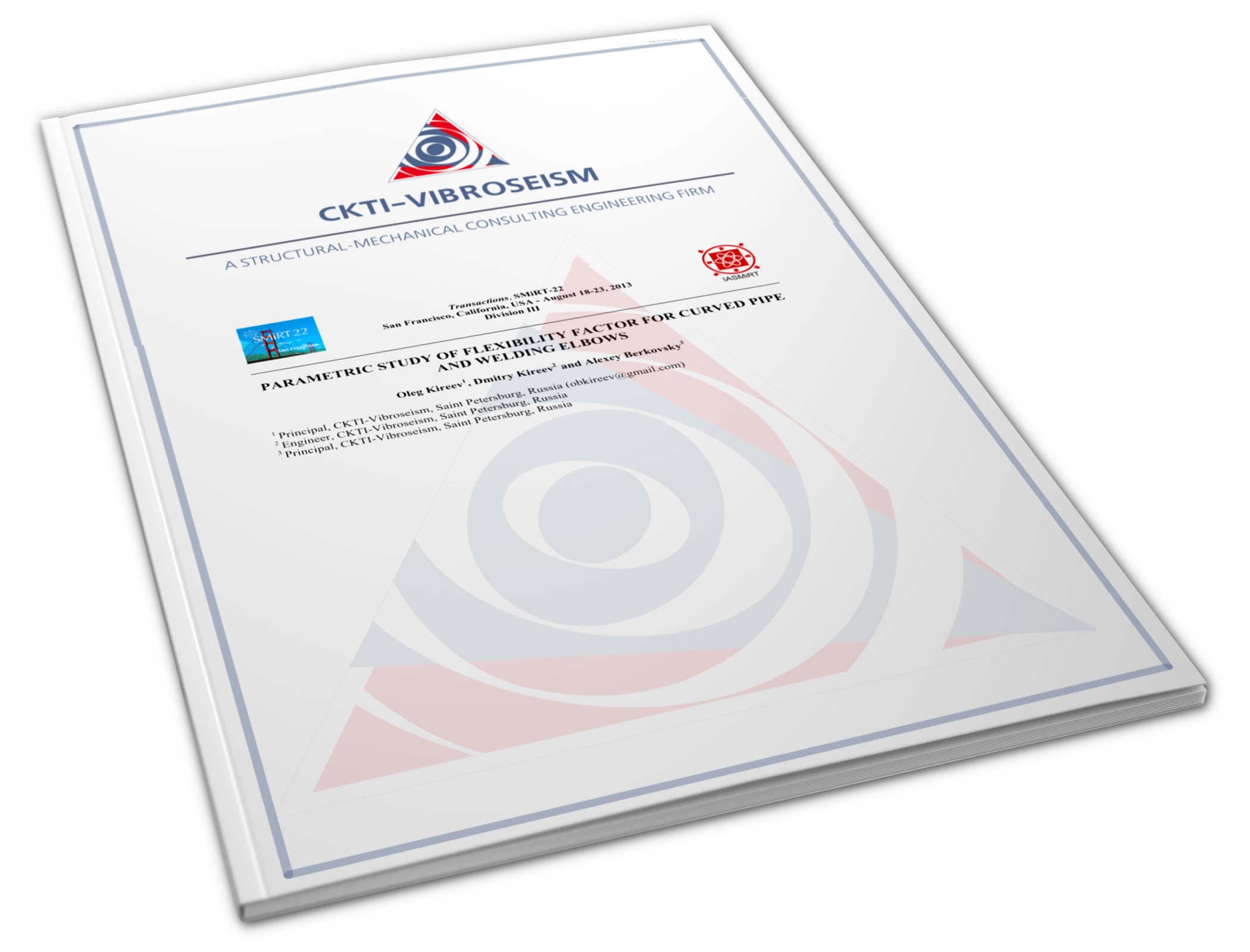
- Autors: : Киреев О.Б. [Oleg B. Kireev], Киреев Д. [Dmitriy Kireev], Берковский А.М. [Alexey M. Berkovskiy]
- Publisher: English
- Pages: 9
- N°: 35
- Library: Conference Papers
- Year: 2013
- File: FLEXIBILITY_PAPER
Hits: 1903
It is known that thin-walled curved pipes or welded elbows under bending exhibit significantly higher flexibility than straight pipe of the same cross-section. To address this phenomena different piping Codes and Standards based on the elementary beam theory introduce in analysis a so called “flexibility factor” for correction of the bending stiffness of the bend elements. The accuracy of these coefficients used in analyses to a large extent determines the precision of the calculated stresses in piping components and loads on the supporting structures and connected equipment (turbines, pumps, etc.).
Despite the fact that behavior of piping bends in operational conditions are well studied, almost all existing piping Codes and Standards establishing flexibility factors for bends do not consider the influence of "end effects" (constraints of the bend ends by the adjacent straight pipes). Chapter NB-3680 of ASME BPVC has for many years contained a note that "The flexibility of a curved pipe or welding elbow is reduced by end effects, provided either by the adjacent straight pipe or by the proximity of other relatively stiff members which inhibit ovalization of the cross section". But nowadays, the only normative document where this effect explicitly is taken into account is the ASME Code Case N-319-3, but its scope is limited by butt welding elbows per ANSI B16.9 and ANSI B16.28 with ratio R/r=2 and 3.
This paper presents results of a finite element study performed to determine the flexibility factors for curved pipes under internal pressure and subjected to in-plane and out-of-plane bending. The influence of end effects are considered as well. The study covers the whole range of geometrical parameters of bends used in design for industry, conventional and nuclear power plants (2<R/r<12, 2<r/t<50, and 15°<<180°). Obtained results can be used to improve the existing regulatory documents related to the stress analysis of nuclear and industrial piping.